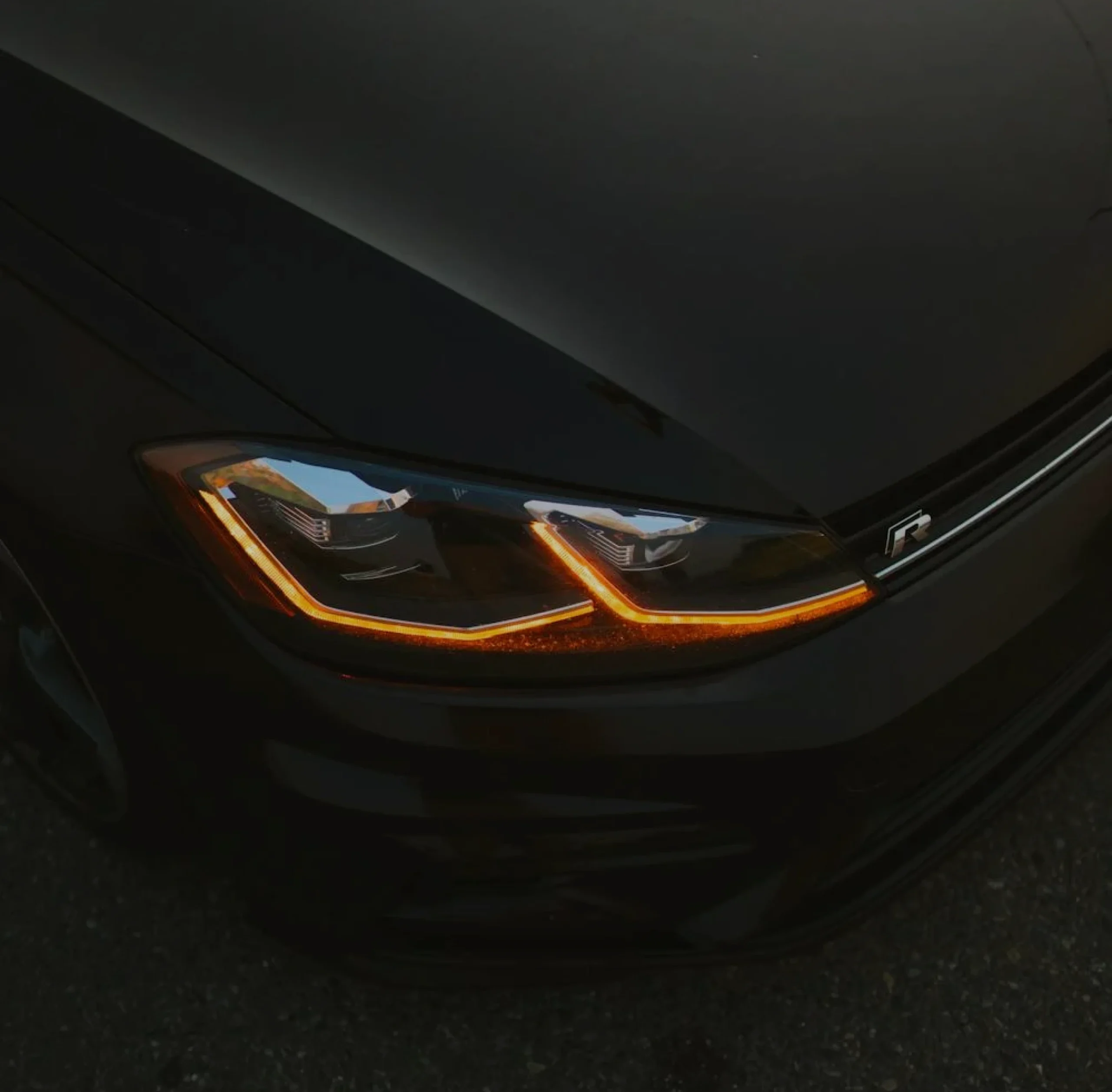
Wprowadzenie
System do wizyjnej inspekcji amortyzatorów został skonstruowany dla jednego z największych producentów w branży motoryzacyjnej.
Wyzwanie
Główne wyzwania stojące przed tym projektem obejmowały kilka krytycznych aspektów. Po pierwsze, konieczne było zapewnienie, że system będzie w stanie dokładnie identyfikować i rozróżniać różne typy amortyzatorów. Zdolność ta miała kluczowe znaczenie dla utrzymania integralności procesu produkcyjnego i zapewnienia, że właściwe amortyzatory były używane we właściwych zastosowaniach.
Po drugie, najważniejsza była weryfikacja poprawności procesu montażu. Każdy amortyzator musiał być prawidłowo zmontowany i spełniać określone standardy, aby zagwarantować jego wydajność i niezawodność. System musiał być w stanie wykryć wszelkie błędy montażowe, aby zapobiec dalszemu rozwojowi wadliwych produktów na linii produkcyjnej.
Kolejnym istotnym wyzwaniem był dokładny odczyt i interpretacja kodów wydrukowanych na etykietach dołączonych do amortyzatorów. Kody te często zawierały ważne informacje o produkcie, a wszelkie błędy w ich odczytywaniu mogły prowadzić do problemów ze śledzeniem i kontrolą jakości.
Ponadto system musiał zapewniać prawidłowe umieszczenie każdej etykiety na amortyzatorze. Prawidłowe umieszczenie etykiet było konieczne zarówno ze względów estetycznych, jak i funkcjonalnych, ponieważ nieprawidłowo wyrównane etykiety mogły wpłynąć na prezentację i użyteczność produktu.
Wreszcie, kluczowe znaczenie miało potwierdzenie, że wszystkie wymagane elementy są obecne i prawidłowo umieszczone na etykiecie. Obejmowało to weryfikację układu i upewnienie się, że wszystkie niezbędne informacje zostały uwzględnione i odpowiednio sformatowane. Brakujące lub nieprawidłowo umieszczone elementy na etykiecie mogą prowadzić do nieporozumień i potencjalnych problemów z identyfikacją i użytkowaniem produktu.
Rozwiązanie
Aby sprostać tym wyzwaniom, wdrożono kompleksowy system kontroli wizyjnej. Ten zaawansowany system obejmował cztery niezależnie działające kamery. Każda kamera była odpowiedzialna za monitorowanie amortyzatorów pod innym kątem, umożliwiając dokładną inspekcję i zapewniając, że żaden szczegół nie został pominięty. To wielokątowe podejście było niezbędne do identyfikacji i rozróżniania różnych typów amortyzatorów, weryfikacji poprawności montażu oraz sprawdzania rozmieszczenia etykiet i elementów.
Ponadto kamery zostały zintegrowane z zaawansowanym procesorem wizyjnym. Integracja ta umożliwiła analizę w czasie rzeczywistym i podejmowanie decyzji w oparciu o obrazy zarejestrowane przez kamery. Procesor wizyjny był w stanie szybko zinterpretować dane, zapewniając, że wszelkie anomalie lub błędy zostały natychmiast zidentyfikowane i usunięte. Ta możliwość działania w czasie rzeczywistym była niezbędna do utrzymania wydajności i dokładności procesu kontroli, zapewniając, że każdy amortyzator spełnia wymagane standardy przed przejściem na linię produkcyjną.
Wyniki
Wdrożenie tego systemu kontroli wizyjnej zaowocowało znaczną poprawą kontroli jakości. Wykorzystanie usług zautomatyzowanej kontroli optycznej (AOI) zapewniło, że każdy amortyzator został skrupulatnie sprawdzony pod kątem wszelkich wad lub rozbieżności. To zautomatyzowane podejście nie tylko zwiększyło dokładność i niezawodność kontroli, ale także poprawiło ogólną wydajność procesu produkcyjnego. System zapewnił producentowi solidne rozwiązanie pozwalające utrzymać wysokie standardy jakości i skutecznie spełniać wymagania branżowe.
Zobacz więcej postów: