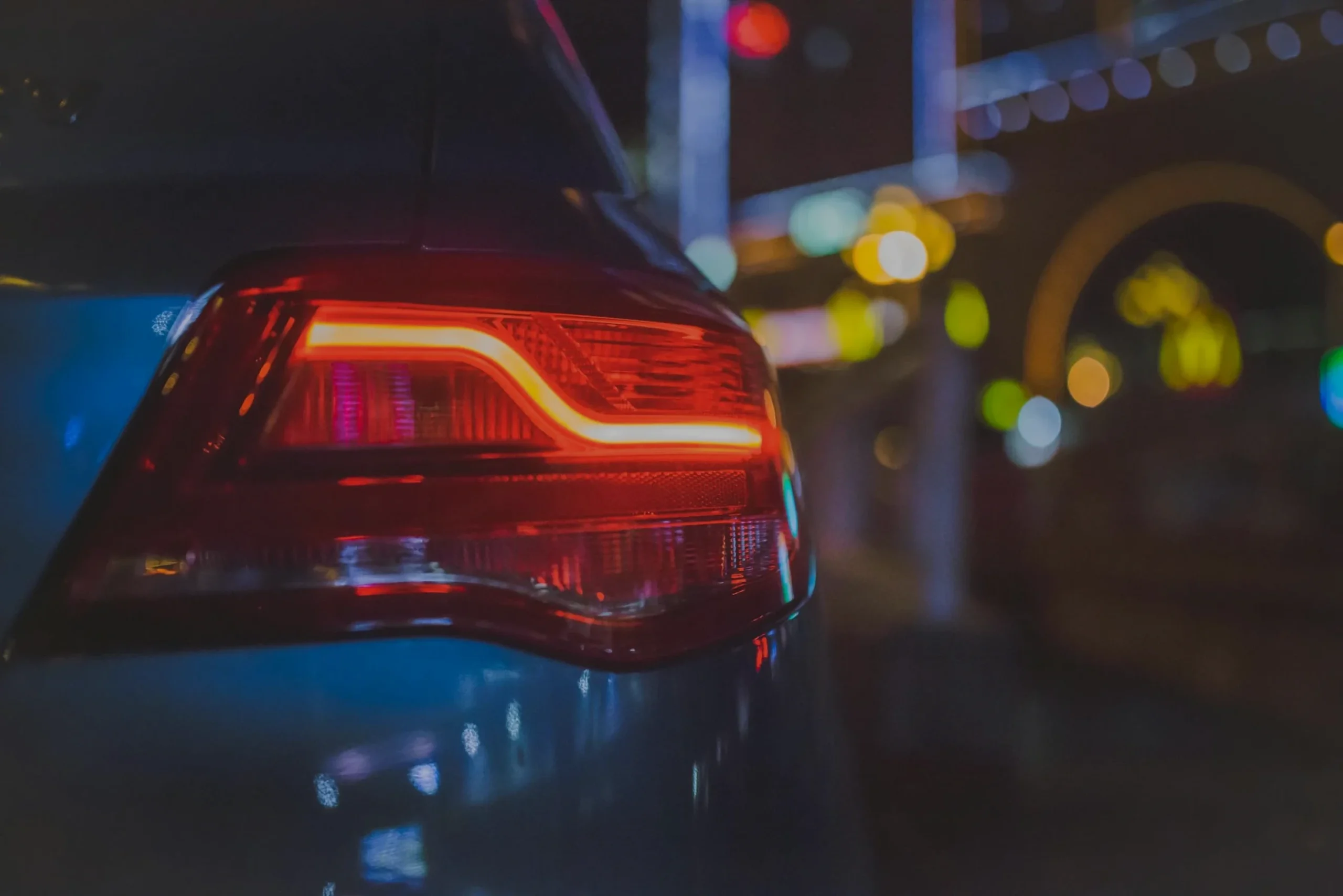
Background
Professional performance of the product optimization service in accordance with the approved specification by highly qualified and experienced employees.
Place of service
Belgium, client’s plant.
The Challenge
Co-operating with experienced partners in the field of quality control, selection and repair has been a standard in the automotive industry for many years. With the development of new technologies and the creation of more complex vehicles, manufacturers are increasingly turning to these services modify and upgrade vehicle that have just left the production line. In these situations, success can only be assured by cooperation with experienced service providers from the automotive industry.
When choosing companies for cooperation, leading car manufacturing companies take into account such factors as the level of specialist knowledge, results obtained on previous projects, flexible adaptation to the needs of customers, the speed of order fulfillment and the company’s structure. So it’s no wonder that Exact Systems was invited to a project to optimize a battery management system for one of the OEMs.
The task set by the client was clear: professional performance of the product optimization service in accordance with the approved specification by highly qualified and experienced employees. The place of the order was the client’s plant. We had a week to prepare all the pieces of this technologically advanced puzzle. The speed of response for the Exact Systems team was not a problem, but the raging COVID-19 pandemic made it necessary to look more closely at the guidelines for crossing borders, the need for quarantine, and compliance with the rules to minimize the risk of disease in the countries that included the project members.
The key issue during its implementation was the selection of appropriate experts. Exact Systems, as a Capital Group, is present in 13 countries, which significantly accelerated the search for people with appropriate qualifications, ready to get involved in this project. This international cooperation gave the company the opportunity to use the extensive knowledge and experience of employees gained in demanding projects in the automotive industry in various parts of the world. Ultimately, to ensure successful implementation, we established a group of 30 highly qualified people with SEP qualifications for the project. Everything was coordinated by our experienced specialists.
We have also committed all employees to the confidentiality of data, therefore the content published below reflects only a small part of our cooperation.
The Solution
The project we undertook was complex and multi-stage, related to the modernization of the car by optimizing the battery management system. The difficulty in carrying out this unusual service action was the fact that it was work with high voltage on the car, at a time when the production process was already finished. The volume of vehicles to be verified was 3,500. There was time to complete each of the 6 stages, which should not be exceeded, and the pace of work at each stage had to be synchronized with the remaining stages.
The preparation process took into account the needs, goals and requirements of the client. It assumed recruitment and logistics activities related to the accommodation of employees close to the place of the order, as well as the issues of ensuring appropriate training and equipment for all involved people. It was the time to develop an action plan, select zones and assign employees to each of them.
The process developed by Exact Systems experts had to ensure the optimization of 80 to 120 vehicles per day in order to meet the deadline set at the beginning. Our experience in similar projects, where time played a key role, helped us to accomplish this task. For the most effective work, the entire process has been divided into six steps.
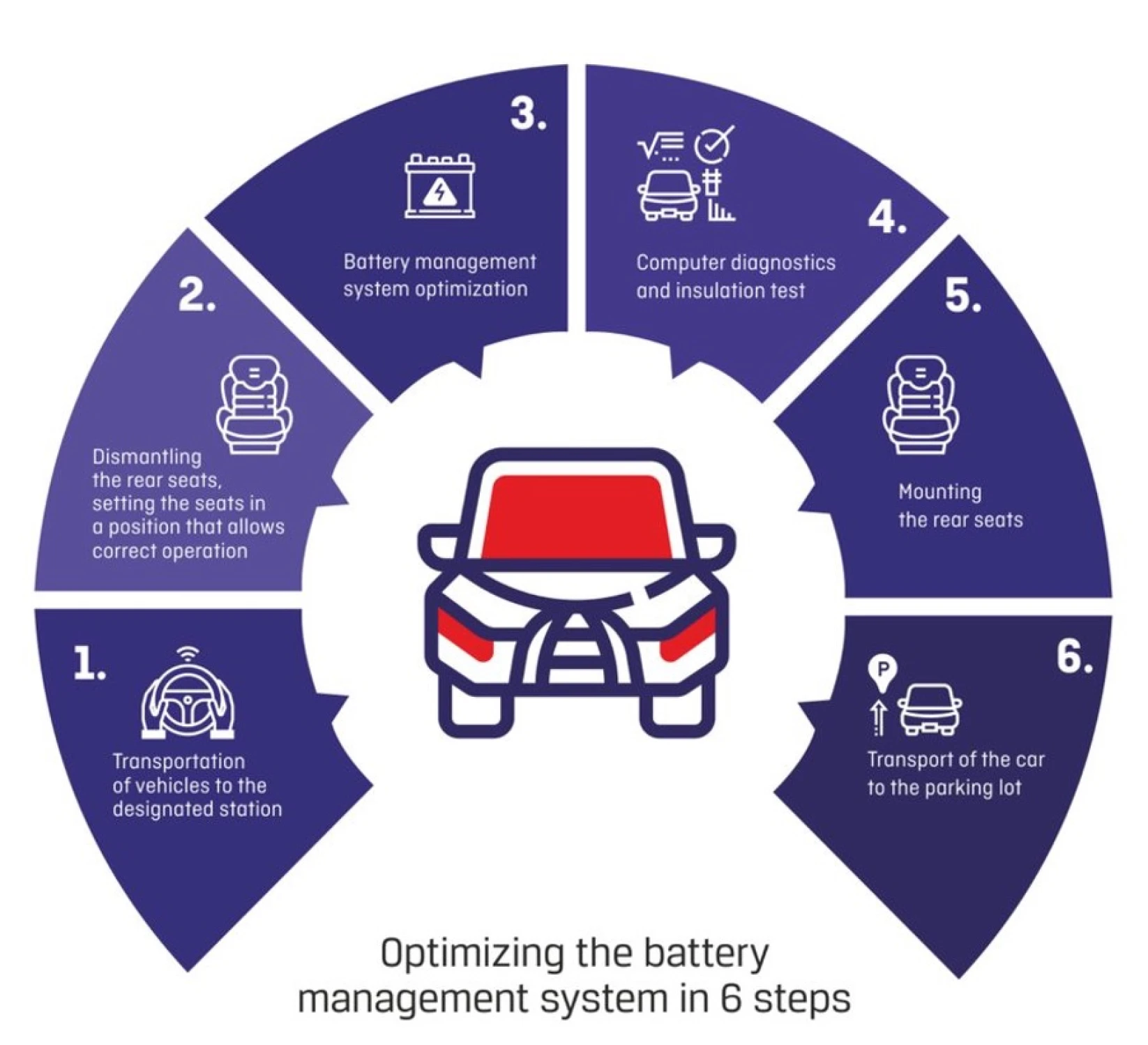
Transportation of vehicles to the designated station
This work had to be carried out with the utmost care. Remember that the battery management system optimization had to be done on the finished vehicle. The key element at this stage of works was safe transport to a designated place in the customer’s facility and skilful unloading of individual vehicles.
Dismantling the rear seats, setting the seats in a position that allows correct operation
At this stage, Exact Systems experts were still preparing for the main part of the task, but none of them could be ignored. The disassembly of the rear seats was carried out according to detailed instructions. The key was to properly secure the seats for the duration of the project, as well as to position the seats in a way that allows for trouble-free performance of the entire operation.
Battery management system optimization
The essence of the whole project! For its implementation to be successful, it was important to follow the prepared instructions, without allowing for any deviations. Exact Systems experts were equipped with appropriate clothing and tools enabling work under high voltage. Further works of the third stage concerned the operation of optimizing battery management by placing additional elements in the structure, after disconnecting battery.
Computer diagnostics and insulation test
Precise control eliminates the risk of defective batches of products, therefore the entire process has been subject to additional checks. Brand-dedicated tools were used in the measurement diagnostics, which is why the diagnostic work was carried out efficiently and without any problems.
Mounting the rear seats
Proper execution of stage 1 guaranteed the success of stage 5. The assembly of the rear seats was carried out with the utmost care and attention to avoiding damage to the material.
Transport of the car to the parking lot
After the assembly of the rear seats was completed, a team of experts transported each vehicle to a designated place in the customer’s facility.
The work of optimizing battery management was like solving an extremely complex puzzle. – says the operational director Dariusz Dengusiak – This task required from us a great technical knowledge and experience in the field of technology, diagnostics, quality and logistics. The more so because, apart from the main operation, we also carried out simpler works related to measuring resistance, setting the lights, or updating vehicle software. Careful planning of each stage, a well-selected, highly qualified team and efficient coordination of the processes made the entire project successfully completed.
Electromobility is an extremely important branch of the European economy. The goals set by Exact Systems in this area are, above all, an even better adaptation to the dynamically changing needs of customers related to the development of technology. Therefore, we focus on optimizing our resources. We attach great importance to the acquisition and retention of experts in this area, as well as the development of employees, whom we have been training for many years as part of the original educational program Quality Academy.
Results
Services we used
See more use cases