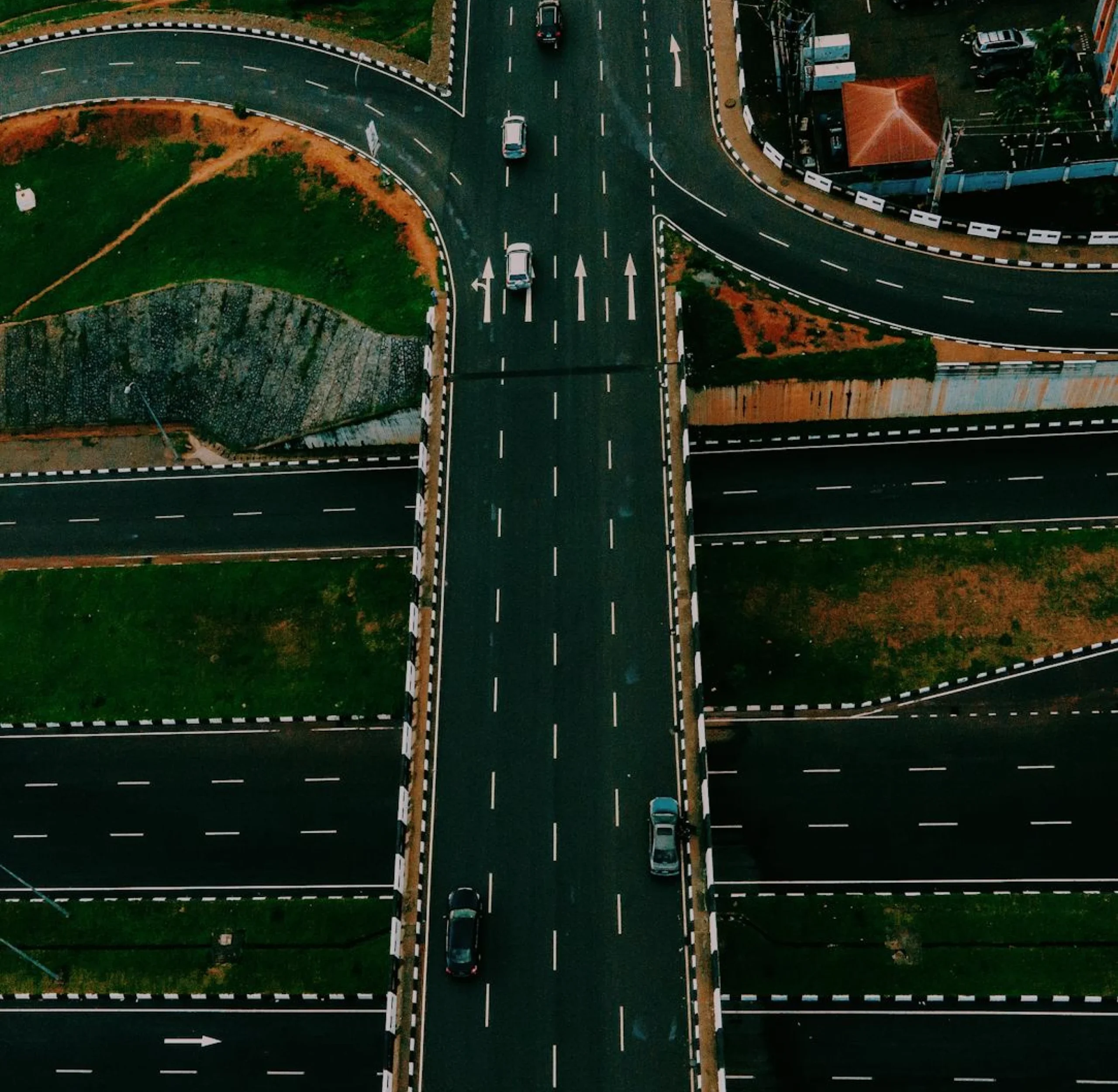
Background
A leading automotive manufacturer, specializing in the production of passenger vehicles, faced the challenge of reworking hazardous parts. The company needed an external partner to manage this process off-site, ensuring that the operation met stringent safety and logistical requirements.
The Challenge
The project presented a number of significant challenges that required careful consideration and strategic planning. First and foremost, the rework service involved handling a product classified as hazardous, which required specialist expertise and strict safety protocols. Ensuring the safe handling, processing and storage of these materials was essential to avoid any potential risks.
In addition, the logistics of operating an off-site rework facility added another layer of complexity. Coordinating the movement of hazardous materials between the customer’s operations and the offsite facility required seamless integration with the customer’s internal systems. Maintaining a smooth and efficient workflow while ensuring that all logistical aspects were meticulously managed was a key challenge.
Compliance with ADR (European Agreement concerning the International Carriage of Dangerous Goods by Road) standards was also essential. The entire process, from loading to unloading, had to adhere strictly to these regulations to ensure the safe and legal transport of the hazardous materials. This added another layer of complexity, requiring thorough planning and precise execution to meet all regulatory requirements.
The Solution
To successfully meet the challenges of this project, a number of strategic solutions were implemented.
Firstly, a robust system was developed to fully integrate the external rework facility with the client’s internal systems and processes. This integration ensured seamless communication and coordination between the two sites, enabling a smooth and efficient workflow in line with the client’s operational standards.
A key aspect of the solution was the preparation of a dedicated external space, equipped with all the necessary elements required for the project’s execution. This facility was outfitted with specialized tools, safety equipment, and technology tailored to handle the hazardous materials involved in the rework process. The space was designed to meet all regulatory requirements, providing a safe and efficient environment for the rework operations. In addition, a comprehensive logistics service was established to manage the entire flow of materials and components between the client’s site and the external facility. This included the transportation, loading, and unloading processes, all of which were meticulously planned and executed to ensure compliance with ADR regulations.
To maintain the highest quality and safety standards, a team of 30 highly qualified inspectors was assembled, all of whom had undergone SEP training. SEP certification is an electrical qualification that allows work on electrical equipment. This team brought the necessary knowledge to handle the hazardous materials involved in the rework process, ensuring compliance with all safety protocols and industry regulations.
In addition, a continuous improvement strategy was put in place to regularly assess and optimize the working time and efficiency of the repair process. By continuously evaluating and improving procedures, the team was able to increase productivity and maintain high performance standards.
Finally, the rework operation was further improved through process optimization. This approach focused on identifying and eliminating inefficiencies, leading to reduced lead times and increased overall productivity in the rework process.
Results
Services we used
See more use cases