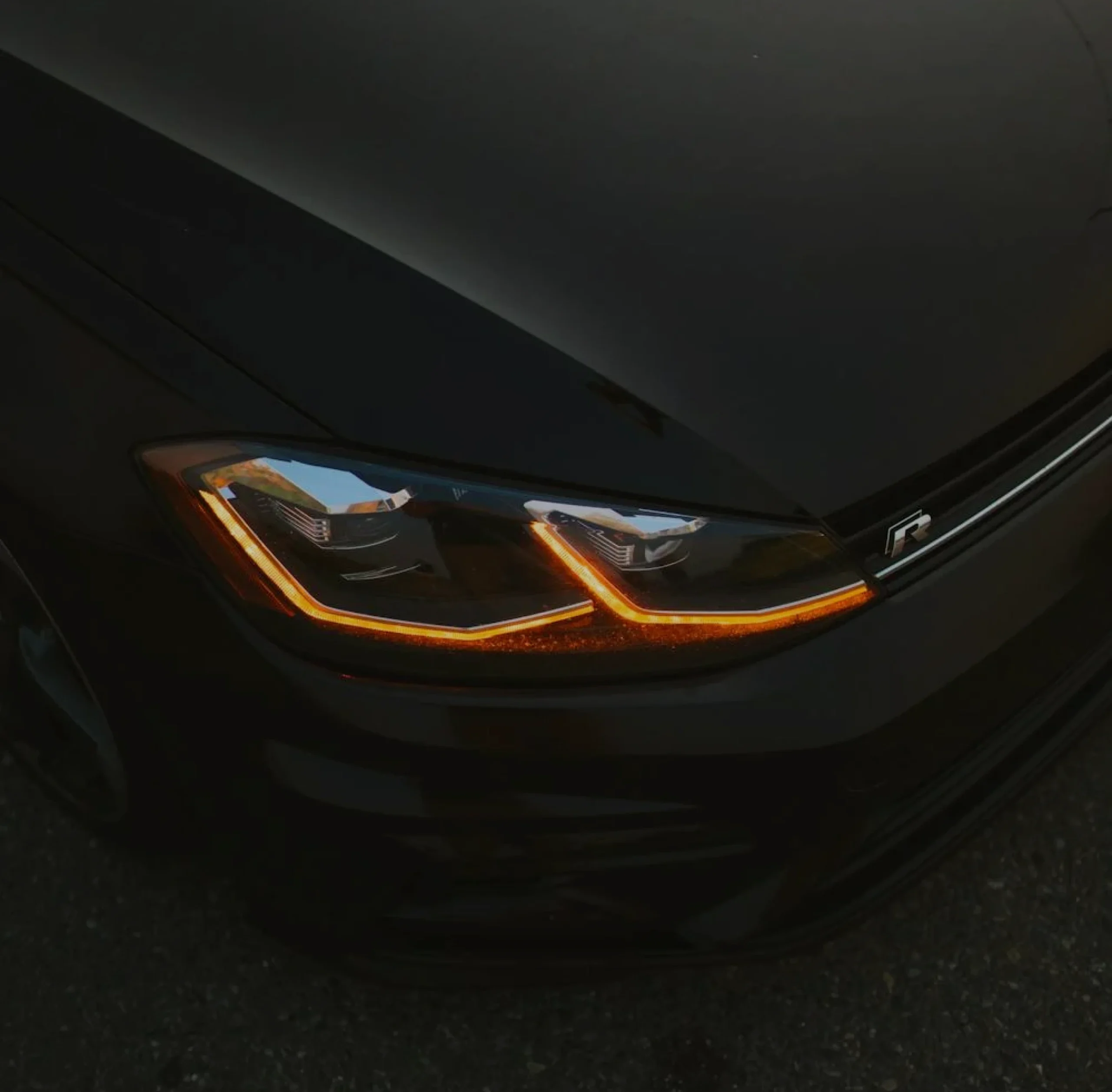
Background
A system for vision inspection of a shock absorber was constructed for one of the largest manufacturers in the automotive industry.
The Challenge
The primary challenges faced in this project included several critical aspects. First, it was essential to ensure that the system could accurately identify and differentiate between various types of shock absorbers. This capability was crucial for maintaining the integrity of the manufacturing process and ensuring that the correct shock absorbers were used in the right applications.
Second, verifying the correctness of the assembly process was paramount. Each shock absorber needed to be assembled correctly and meet the specified standards to guarantee its performance and reliability. The system had to be capable of detecting any assembly errors to prevent defective products from progressing further in the production line.
Another significant challenge was accurately reading and interpreting the codes printed on the labels attached to the shock absorbers. These codes often contained important information about the product, and any errors in reading them could lead to issues in tracking and quality control.
Additionally, the system needed to ensure that each label was correctly positioned on the shock absorber. Proper label placement was necessary for both aesthetic and functional reasons, as misaligned labels could affect the product’s presentation and usability.
Lastly, confirming that all required elements were present and correctly placed on the label was crucial. This included verifying the layout and ensuring that all necessary information was included and properly formatted. Missing or incorrectly placed elements on the label could lead to confusion and potential issues in product identification and use.
The Solution
To overcome these challenges, a comprehensive vision inspection system was implemented. This advanced system featured four independently operating cameras. Each camera was responsible for monitoring the shock absorbers from a different angle, allowing a thorough inspection and ensuring that no detail was overlooked. This multi-angle approach was essential for identifying and differentiating between different types of shock absorber, verifying correct assembly and checking label positioning and elements.
In addition, the cameras were integrated with an advanced vision processor. This integration enabled real-time analysis and decision making based on the images captured by the cameras. The vision processor was able to interpret the data quickly, ensuring that any anomalies or errors were identified and addressed immediately. This real-time capability was essential to maintaining the efficiency and accuracy of the inspection process, ensuring that each shock absorber met the required standards before moving on to the production line.
Results
The implementation of this vision inspection system resulted in significant improvements in quality control. The use of Automated Optical Inspection (AOI) services ensured that every shock absorber was meticulously inspected for any defects or discrepancies. This automated approach not only increased the accuracy and reliability of the inspections but also enhanced the overall efficiency of the manufacturing process. The system provided the manufacturer with a robust solution to maintain high-quality standards and meet industry requirements effectively.
See more use cases